KiBaTest - Artificial Intelligence for battery testing
Project Completed - Contact: ftm(at)ftm.mw.tum.de
Problem
When designing a battery system, care must be taken to ensure that a large number of requirements, such as range, performance, safety, reliability and service life, are also met in practice. In order to ensure that these requirements and applicable standards are met, extensive and cost-intensive test bench trials are currently being carried out. On the one hand, these are tests within the operating specifications (performance tests), such as test series to characterise the ageing behaviour of a battery. On the other hand, tests are carried out outside the specifications (Abuse Tests) in which the reaction of a battery is tested in the event of misuse.
Especially ageing test series, in which batteries are iteratively cycled to their end of life, can take several months and thus occupy costly test facilities for a long period of time. In addition, the tests have to be carried out at cell, module and pack level, which increases the testing effort enormously. The increasing degree of complexity from the individual cell to the pack increases the test costs incurred, caused by the test item itself, but also by the test equipment (devices, premises, protective facilities, etc.). All in all, the current battery testing process is therefore associated with a high time and financial outlay.
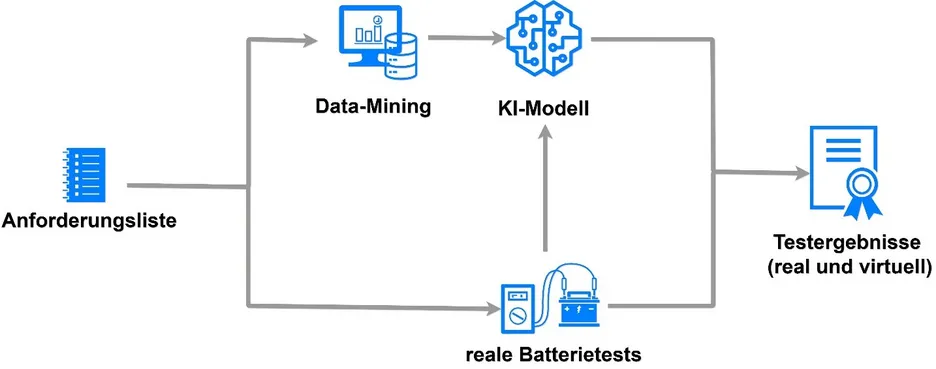
Aim
The basic aim of this project is to optimise the testing of battery systems through the use of artificial intelligence. For this purpose, a semi-virtual assurance process is to be developed in which a symbiosis is entered into between the still necessary real-physical tests and artificial intelligence. Through a clever interplay of physical testing and Big Data analyses, an increasingly virtual assurance process is to be made possible. This should considerably facilitate integration into the product development process of vehicles, which would ultimately have a positive effect on faster market penetration of electrified vehicles. An extended understanding of the developed battery systems can already be built up in the pre-series phase, resulting in a better prediction of the battery's behaviour within its service life. Among others, the following aspects can be improved by intelligent testing:
- Safety: By simulating additional accident scenarios, the safety of the developed battery systems can be better evaluated - without additional costs.
- Sustainability: Knowledge of the performance under different environmental conditions and simulation of these makes potential reuse of the test samples possible and plannable.
- Cost-effectiveness: Warranty in markets, e.g. where climatic conditions are unfavourable for the battery system (hot/cold countries), can cause high costs. Through the extended virtual testing, extensive key data can be generated for scenarios of the most unfavourable conditions in order to better estimate and reduce the future costs of a system failure in the field.