OptiPro - Optimierte Zellfinalisierung durch innovative Anlagentechnik und parametergestützter Auswertung der Prozess- und Qualitätsparameter im virtuellen Produktionssystem
Ansprechpartner: Manuel Ank, M.Sc. (ab 01.09.2024: EV Teamleiter)
Problemstellung
In den Prozessschritten der Zellfinalisierung wird die Produktion von Lithium-Ionen-Batteriezellen abgeschlossen. Die Zellfinalisierung in der Batteriezellproduktion ist bisher durch Limitation des erzielbaren Durchsatzes und unzureichend bekannter Beeinflussung der Zellqualitätsparameter gekennzeichnet. Dies spiegelt sich unter anderem in langen Prozesszeiten und hohen Fertigungskosten wider.
Ziel
Das Ziel des Forschungsvorhabens ist eine optimierte Zellfinalisierung durch innovative Anlagentechnik und parametergestützter Auswertung der Prozess- und Qualitätsparameter im virtuellen Produktionssystem (OptiPro) zu realisieren. Hierfür soll die gesamte Prozesskette der Zellfinalisierung auf dem aktuellen Stand der Technik digitalisiert werden. Dies bedeutet, dass innovative Messtechnik verwendet wird, um eine parametergestützte Auswertung der Prozess- und Qualitätsparameter des jeweiligen Prozessschritts zu ermöglichen. Die Abbildung der Daten soll in einem virtuellen Produktionssystem erfolgen und mittels künstlicher Intelligenz (KI) analysiert und ausgewertet werden. Alle verwendeten Anlagentechniken innerhalb der Zellfinalisierung sollen zwischen dem realen und dem virtuellem Produktionssystem so kommunizieren, sodass ein dauerhafter Feedback-Loop entsteht.
Die großen Energie- und Ressourcenbedarfe einiger Teilschritte (u.a. Befüllen, Formieren, Testlagern und End-of-line Test) motivieren dazu Prozesszeiten zu minimieren. Der Materialbedarf stellt einen signifikanten Kostentreiber dar, in der Folge wird ein gezieltes Reduzieren des Ausschusses durch die Optimierung der Prozesse angetrieben. Durch den Informationsaustausch zwischen realen und virtuellen Anlagen soll eben dieses Bestreben zu geringeren Prozesszeiten und Qualitätssteigerung erreicht werden.
Durch das Forschungsvorhaben besteht somit ein großes Potential die Attraktivität für eine kompetitive Batterieproduktion in Deutschland zu stärken, indem die Zellfinalisierung ganzheitlich beeinflusst wird.
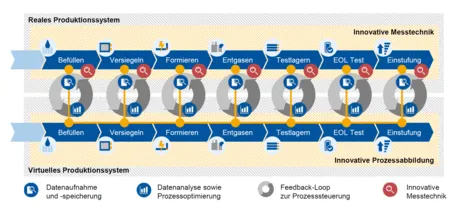
Durchführung
In dem Forschungsprojekt leistet der Lehrstuhl für Fahrzeugtechnik einen entscheidenden Beitrag bei der anwendungsspezifischen Definition des Zielbilds und fokussiert die Forschungsaktivitäten auf die Durchführung und Optimierung der End-of-Line-Prüfung (EOL) und nachgelagerten Validierung der Methoden und Modelle durch umfangreiche Lebensdauertests. Ziel ist es, durch prozessübergreifenden Einsatz inlinefähiger Messtechnik, neuen Messmethoden und einer modellbasierten Verknüpfung deutliche Prozesszeitreduzierungen der EOL-Prüfung zu erreichen und damit
- geringere Durchlaufzeiten einzelner Prozessschritte zu erzielen,
- frühzeitig bereits fehlerhafte Zellen zu identifizieren und auszusondern und
- präzisere Kennzahlen für die Zellqualität zu erreichen,
um folglich den Ressourceneinsatz zu minimieren und damit die Kosten der Produktion zu senken. Die messtechnische Verknüpfung innerhalb eines virtuellen Produktionssystems ermöglicht zudem eine optimierte Steuerung und Regelung der Prozessschritte, um durch echtzeitfähige prozessübergreifende Regeleingriffe langfristig die Qualität der Produktion zu steigern.
Projekteinordnung

Das Projekt ordnet sich im BMBF-Kompetenzcluster 'Intelligente Batteriezellproduktion' (InZePro) ein. Im Fokus steht hierbei die Erhöhung und Flexibilisierung der Produktivität der Zellproduktion. Erreicht werden soll dies durch eine ganzheitliche Optimierung des Produktionssystems unter Einsatz von Lösungen der Industrie 4.0. Schwerpunkte sind dabei: Innovative agile Anlagentechnik, Digitalisierung, Künstliche Intelligenz (KI) in der Produktion sowie virtuelle Produktionssysteme. Mehr Infos hier.
Projektpartner
Im Batterie-Kompetenzcluster „Intelligente Batteriezellproduktion“ (InZePro) wurde die Förderung des Forschungsvorhabens durch das Bundesministerium für Bildung und Forschung (BMBF) beschlossen. Hierbei forschen das Institut 'Production Engineering of E-Mobility Components' der Rheinisch Westfälischen Technischen Hochschule Aachen (PEM - RWTH), das Institut für Stromrichtertechnik und Elektrische Antriebe der Rheinisch Westfälischen Technischen Hochschule Aachen (ISEA - RWTH), der Lehrstuhl fürInformationsmanagement im Maschinenbau der Rheinisch Westfälischen Technischen Hochschule Aachen (IMA - RWTH), das Institut für Werkzeugmaschinen und Betriebswissenschaften der Technischen Universität München (iwb - TUM) sowie der Lehrstuhl für Fahrzeugtechnik der Technischen Universität München (FTM - TUM) im Verbund.
Dieses Forschungsprojekt wird mit Mitteln des BMBF gefördert (Förderkennzeichen: 03XP0364B) und vom Projektträger Jülich betreut. Die Verantwortung für den Inhalt dieser Veröffentlichung liegt beim Autor.



